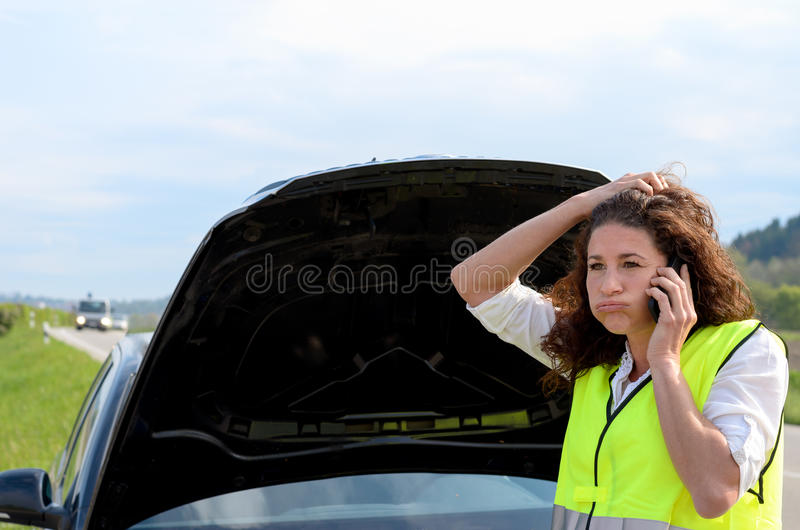
The vehicle’s loaded, you set up 14 of your 15 count locations and… you run out of gear! You were minutes away from wrapping up the workday, but now you have to drive back to the office. Or, if you’re lucky, run into a nearby hardware store to get what you need. We’ve all been there.
Whether it’s due to forgetting equipment in the office, having beat up gear that doesn’t work, or accidentally breaking something in the field, these failures are avoidable.
Through 20+ years of data collection experience at Spack Solutions, we’ve eliminated these issues with three easy steps –
-
Monitoring of equipment and accessories – Traffic data collection equipment sits outside and experiences wear and tear through its lifecycle. To minimize equipment failures, we continually monitor and examine our equipment and accessories.
- Daily Monitoring includes putting any broken or questionable gear in a separate bin in the work vehicle. This stuff could consist of an uncharged camera, an extension pole that won’t extend, or a mounting bracket that’s broken. Then they either get thrown away or tested/repaired back at the shop.
- Weekly Monitoring builds on the daily items and is a general review. This weekly check includes cleaning and ensuring the fieldwork storage area remains organized and determining if any new accessories are needed to keep up stocking levels.
- Annual Checks is where we complete our in-depth clean/check of equipment. We empty all bins and throw out anything questionable. This review includes oiling sticky padlocks, putting tube counters through a tube simulator test, organizing and sorting nails/spikes/pins, checking all pole mounts for broken flanges, pressure testing all road tubes to make sure they don’t have leaks, and spot checking cameras from our stock for runtime. This check ensures nothing slips through the daily/weekly checks. It’s effectively our ‘Spring garage cleaning’ (though we usually do this during our downtime over the winter holidays).
- Maintaining a clean and organized storage area – As much as it pains me to admit it, our parents were right (GASP!), a clean and organized room, or in this case office, helps pave the way to success. Staying neat and orderly extends from work vehicles to office/shop storage spaces. By using designated storage areas, labels, and bins, we set up a clean area where we know where equipment is. Using a bin system allows us to easily see when an accessory item is running low, reducing the chances of having data collection held up due to insufficient supplies. It also speeds up the shop/office work before and after data collection projects.
- Always bring extra equipment to the field – We always bring additional equipment and accessories into the field. The amount of extra gear we take depends on the specific item and the chances of potential failure, but a general rule of thumb is that you should have 10-20% more equipment than you think you need. You only need a couple of extra items that have low failure rates, like extendable poles or locks. But you want dozens of additional accessories that have a limited lifespan, like nails and hose clamps. You might as well have extra bins and buckets of the small accessory items. Finally, we keep a backup stash of smaller accessories items in the work vehicle, including the plastic pole mounts used to attach the CountCAM2 to the adjustable pole, CountCAM2 data port covers to ensure the camera is watertight, lock brackets, and extra booster-to-camera cables. Though we usually catch broken gear during our daily or weekly checks, it comes in handy to have a few extras of everything just in case you slam something in the car door or lose something in the weeds on the roadside. We also keep a backup phone in the vehicle and extra chargers just in case.
We’ve significantly reduced our failure rate, increasing our efficiency and capacity, with these three easy steps and encourage you to develop similar systems for your fieldwork.